INTRODUCTION TO AIoT
The Artificial Intelligence of Things (IoT) is the combination of artificial intelligence (AI) technologies and the Internet of Things (IoT) infrastructure. AIoT aims to create more efficient IoT operations, improve human-machine interactions and enhance data management and analytics.
AI is the simulation of human intelligence processes by machines, especially computer systems, and is typically used in natural language processing, speech recognition and machine vision.
IoT is a system of connected devices, mechanical and digital machines, or objects with unique identifiers with the ability to transfer data over a network without requiring human-to-human or human-to-computer interaction.
The main objective of this technology is to maximize the benefits of IoT by relying on Artificial Intelligence.
INPLANT LOGISTICS
In-plant logistics involves managing and coordinating material movement within a company’s manufacturing plant. It involves the planning, execution, and control of the flow of raw materials, components, and finished goods within the plant. The goal of in-plant logistics is to optimise the use of resources and minimise waste while ensuring the timely delivery of materials to production lines and finished products to the warehouse.
The following three factors are all of major importance in in-plant logistics:
- The infrastructure: By ‘infrastructure’, and in the context of in-plant logistics, we mean the physical facilities of the plant. At the time of a plant start-up, the business will pay special attention to the building because it’s such a large cost for the company, if not the biggest. Unfortunately, often the manufacturer will only plan the workflow and layout after the construction of the building has been completed, but there must be space for flexibility and customisation.
- Organisation: The organisation of the building has a significant impact on the workflow and should be designed for shorter lead times and optimised movement of inventory.
- System: ‘System’ refers to the storage and handling systems the manufacturer uses in their logistics. The equipment they use must be based on the requirements of the activity. Here, warehouse management systems (WMSs), radio frequency (RF) technology and the integration of barcodes with an ERP system all come into their own. They can provide almost completely accurate data on the operator’s workforce, inventory and order location. Their value is immense.
The benefits of in-plant logistics
Managing the logistics inside your plant well is essential to have following benefits:
- Greater productivity.
- Higher levels of efficiency, as operators will work more orderly, in more comfort, and with the help of some automation.
- More control over the pieces. You will know how many there are and where they are in the plant at each moment of the process.
- Achievement of customer loyalty because the final recipient will be receiving the goods on time.
- Lower costs because we make the right errors quickly that would harm the operation of the plant.
HOW AIoT PLAYS A CRUCIAL ROLE IN IN-PLANT LOGISTICS
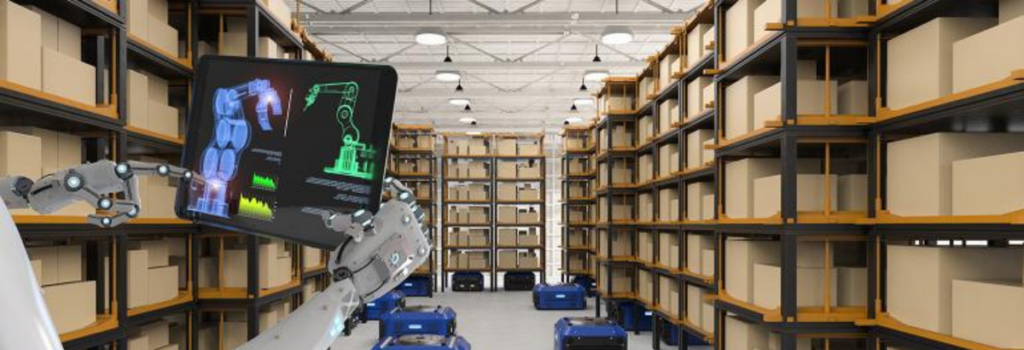
Logistics warehouses are facing increasingly complex challenges, requiring higher productivity and lower error rates. To address these issues, Artificial Intelligence of Things (AIoT) is being implemented in the supply chain. According to a 2020 report by MHI, 60% of companies surveyed plan to use AI within the next five years. Moreover, Business Insider predicts that by 2025, there will be over 64 billion IoT devices, a 540% increase from 2018.
Why it matters
- Manufacturing software and hardware providers have the opportunity to infuse AI-based features into existing offerings.
- Manufacturers who adopt AIoT solutions wisely are witnessing increased efficiency, higher product quality, and smoother processes.
Here we explain some use cases of AIoT in Manufacturing and how those use cases are reducing costs and time and increasing safety. Artificial Intelligence encompasses a wide variety of different technologies that manufacturers can benefit from. The key business outcomes and use cases of AIoT are:
• Production outsourcing
• Design of storage and handling solution
• Packing
• Container Management
• Transportation Management
• Scheduling and dispatch
In this Article we analyze the AIoT and highlight its main applications in the IN-PLANT LOGISTICS: from greater productivity to the introduction of an automated order prep system.
1.production outsourcing
- Power quality meter
Integrated circuits and reference designs help you accelerate development of power quality meters, improving accuracy, responsiveness and connectivity while providing enhanced power quality analysis that protects sensitive equipment.
Design requirements
Power quality meter designs often require:
- Real-time analysis of power quality.
- Reliable wired or wireless connectivity in challenging factory environments.
- Accurate energy measurement and compliance with IEC standards.
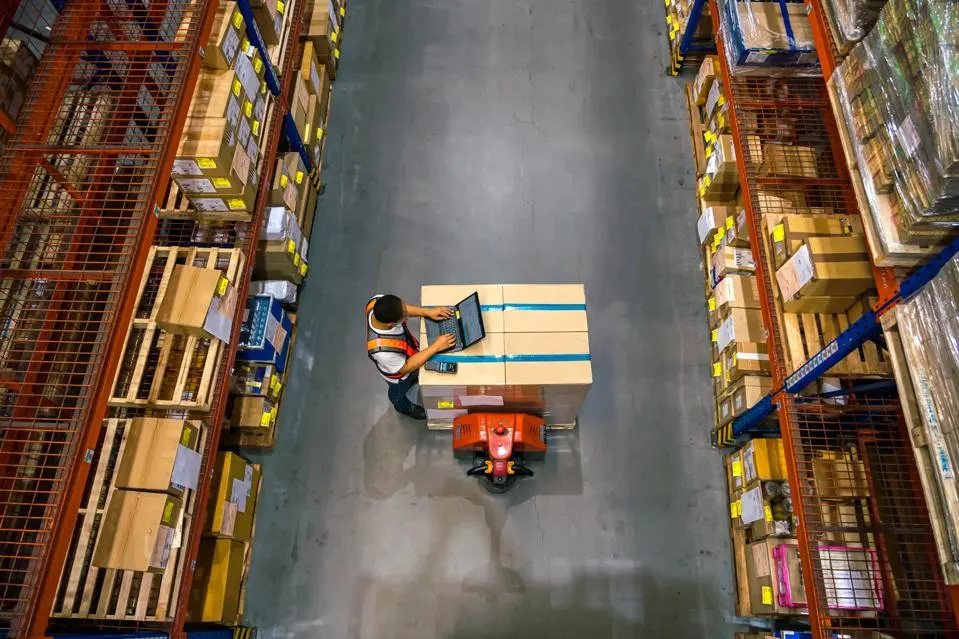
2.Design of Storage and handling solution
Here are some devices and technologies that can be used for the design of storage and handling solutions in inplant logistics with AIoT:
- automated storage and retrieval system
An automated storage and retrieval system (ASRS or AS/RS) consists of a variety of computer-controlled systems for automatically placing and retrieving loads from defined storage locations.[1] Automated storage and retrieval systems (AS/RS) are typically used in applications where:
- There is a very high volume of loads being moved into and out of storage
- Storage density is important because of space constraints
- No value is added in this process (no processing, only storage and transport)
- Accuracy is critical because of potential expensive damages to the load
An AS/RS can be used with standard loads as well as nonstandard loads,[2] meaning that each standard load can fit in a uniformly-sized volume
AS/RS technology varies substantially and can consist of shuttles, cranes and aisles, Autonomous Mobile Robots (AMRs), horizontal and vertical carousels, Vertical Lift Modules (VLMs), Micro-Loads, Mini-Loads, Unit-Loads, stockers, or other systems. It is often integrated with a Warehouse Execution Systems software (WES), Warehouse Management Systems software (WMS), Warehouse Control Systems software (WCS) or other software and controls.
- Predictive Maintenance :
Smart predictive maintenance is a powerful tool that can help organizations reduce costs, improve reliability, optimize maintenance schedules, increase safety, and facilitate data-driven decision-making. By leveraging advanced technologies and data analytics, smart predictive maintenance can predict equipment failures, schedule maintenance proactively, and prevent unexpected breakdowns. This approach minimizes downtime, saves on emergency repairs, and extends the lifespan of equipment.
Machine Learning (ML) can be used to implement predictive maintenance algorithms and models directly on edge devices, such as sensors or IoT devices, rather than relying on a centralized cloud- or server-based system. This approach offers several benefits, including reduced latency, improved real-time decision-making, enhanced data privacy, and reduced bandwidth requirements.
From designing smart sensor nodes and configuring embedded software running in sensor nodes and the gateway, to developing software to be integrated into the Cloud or company Enterprise Resource Planning (ERP) system, Predictive Maintenance requires a variety of skills and competencies. With Machine Learning and Artificial Intelligence algorithms, technical anomalies can be detected early, and equipment uptime can be maximized.
Smart sensor nodes play a vital role in predictive analysis; they collect and log pre-processed, secure data to be displayed in visualization tools and used in other processing algorithms. Smart sensor nodes can also process data and detect anomalies by reducing computational latency.
Gateways can either be implemented to collect and process data from several smart sensor nodes or to act as a connectivity bridge to enable secure connection to the cloud using Ethernet, Wi-Fi, cellular, or LPWAN technologies.
Companies are adopting AI-powered machines and algorithms to develop more intelligent packaging solutions. The use of 3D printing is becoming increasingly prevalent in industrial applications, affecting not only designers but the entire supply chain. The packaging industry will undergo significant changes as a result of these new technologies. Here are ten of the numerous innovations that will impact the packaging industry:
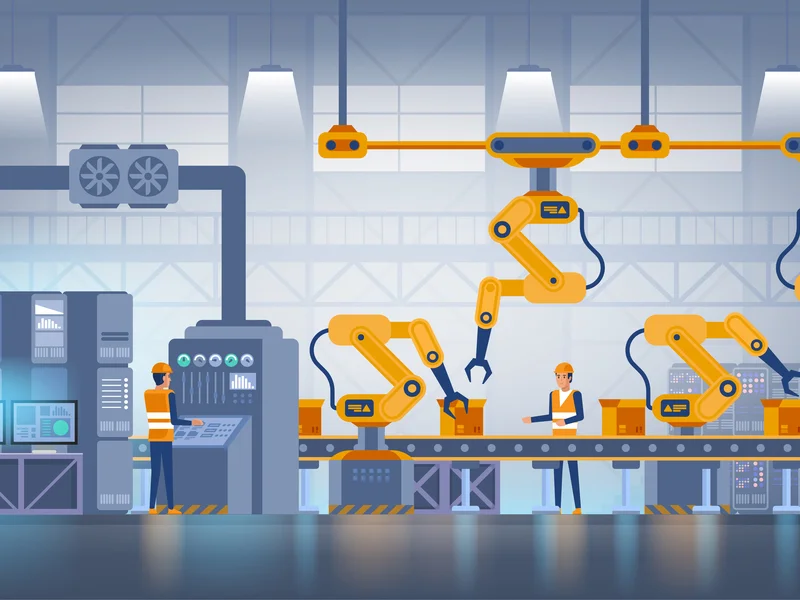
1) AI will generate packaging prototypes in 3D space.
Artificial intelligence (AI) is a promising technology for development and design. It can create prototypes without human intervention, which helps save time and resources. However, it’s important to note that the AI can only generate a three-dimensional prototype. If the product requires assembly, then it is necessary to program it into the algorithm. It’s not as simple as letting the AI operate freely on your CAD files without proper instructions. Therefore, it’s important to give clear instructions to the AI to ensure that the prototype is accurate and meets your requirements.
2) AI will design a package that is tailored to the product’s needs.
Designers are already utilizing virtual reality and augmented reality headsets to create packaging designs. This technology can also be combined with AI to create algorithmically designed packaging that is tailored to specific products, as computing power continues to advance.
3) AI will create packages of different shapes and sizes for specific products.
The design of product packaging can be altered to some extent, but with the advent of artificial intelligence, a wider range of possibilities will become available. For instance, AI can be used to create packages that are tailored to fit specific products, such as cereal or hot dogs, in different shapes and sizes. However, when creating custom packaging shapes, specific machine parts must be produced using CNC milling. Customization is essential in packaging since it fosters customer loyalty by providing a personalised feel to the package. This level of customization also instils trust in the manufacturer of the product, as they have gone out of their way to create bespoke packaging just for the customer.
4) Packages will include RFID tags or QR codes to communicate and reorder groceries.
The RFID tags and codes will need to be incorporated into the packaging design to enable smart feature compatibility. This added element could increase packaging costs but might need to be considered in the design phase.
5) AI-driven automation will help companies reduce manufacturing costs by directing and controlling robots.
Machines need to be accurately programmed with precise instructions in the manufacturing process, but AI-driven automation is capable of performing tasks without precise instructions. AI is also used for quality control. The ability of machines to self-diagnose problems with a system or component prior to human intervention can lead to improved efficiency as well as decreased downtime. This could potentially lead manufacturers to produce more flexible products in smaller batches that are personalized based on each customer’s specifications. The flexibility offered through customization would allow customers greater choice while ensuring product consistency across all orders, which should improve customer satisfaction levels.
6) Packages will sense any tampering and alert authorities accordingly.
This will help protect companies from misuse of their products, for example, the sale of stolen goods or counterfeit content. The technology is also expected to help detect when packages have been dropped in transit, which has a high risk of damaging them.
7) Artificial intelligence will optimize production lines and increase the efficiency of packaging processes.
This way, companies can generate higher profits by reducing labor costs and increasing output. Machines with AI are also more precise than humans when it comes to processing data quickly and efficiently. Some studies show that they only need around 20% as much time to learn something new compared to a human counterpart. In this sense, automation is already happening, but in an effortless fashion for many people — primarily because there’s not enough awareness about the issue at play here: whether or not artificial intelligence should replace human jobs.
8) Sustainable practices will be at the forefront of packaging manufacturing with AI.
AI will help the packaging industry accelerate its transition to sustainable practices by enhancing supply chain and inventory management, optimizing distribution routes, and tracking products during transit. AI can predict demand and consumption and streamline the manufacturing process. This reduces waste during manufacturing. AI can also generate alternative packaging solutions that reduce complexity and required resources.
9) Artificial intelligence will prevent downtime with preventative maintenance.
The number-one reason for packaging machine downtime is unplanned maintenance. Machines malfunction because of wear and tear, or when they are not used correctly over time. This can lead to lost hours in a week that cannot be recovered due to insufficient human labor at the factory level. Artificial intelligence could help identify problems before they occur, helping prevent downtime from occurring.
10) The use of augmented reality (AR) and virtual reality (VR) headsets will allow consumers to see what’s inside the package without opening it.
Virtual reality will soon be a normal part of the customer experience and packaging design process for many companies, as it becomes more affordable for small businesses to invest in immersive VR headsets like Oculus Rift or HTC Vive. This technology is currently being implemented at major retailers such as Target, Walmart, and Home Depot who have experimented with incorporating VR into various aspects of their business, from training new employees in simulated store layouts to helping customers visualize what living room furniture would look like in their house. As this technology becomes mainstream within these industries, we can expect that other sectors of retail will follow suit over the next few years.
4.Container Management
RFID Usage Concepts for Waste Management
RFID technology can improve the efficiency of waste management operations. The process starts with an RFID transponder or tag that should be protected from harsh environmental conditions by embedding it in a rugged plastic housing or container. The tag is attached or embedded in the waste container, and as the container is emptied, the RFID reader and antenna integrated into the waste vehicle reads the tag’s unique serial number.
The unique number can be linked with a date/time stamp, weight of the container, type of container, and customer information. The information can then be sent wirelessly to a server, stored in the reader, or transferred later to a central waste management system. Additionally, the vehicle-mounted tag can identify the waste vehicles themselves, automating hauler, landfill or recycling station operations.
Unlike barcodes, RFID tags do not require direct line of sight and are more durable in harsh waste and recycling environments. They provide a permanent and superior form of unique identification.
Using RFID technology, waste haulers can automate waste collection, container management, and provide verification of service. This information can also help optimize truck usage and routes for maximum efficiency.
- Smart Container :
Smart Containers are ISO containers that come equipped with Internet of Things (IoT) technologies and various sensors and devices. These sensors can detect events like door openings or impacts, offer precise GPS positions and container orientation, measure temperature, pressure, humidity, and luminosity, and determine the presence of volatile organic compound gases, among other things.
The data collected by the Smart Container’s sensors is transmitted to a central monitoring platform known as the Smart Container’s control tower. This platform provides a comprehensive view of the container and its contents, using additional information sources such as Automatic Identification System (AIS) data, as well as data from freight forwarders and other shipping partners.
Smart containers help track important data like:
- container geolocation,
- temperature fluctuations,
- geofencing and predictive ETA,
- shock detection,
- door open/close status,
- late in/out site,
- any unusual activity, etc.
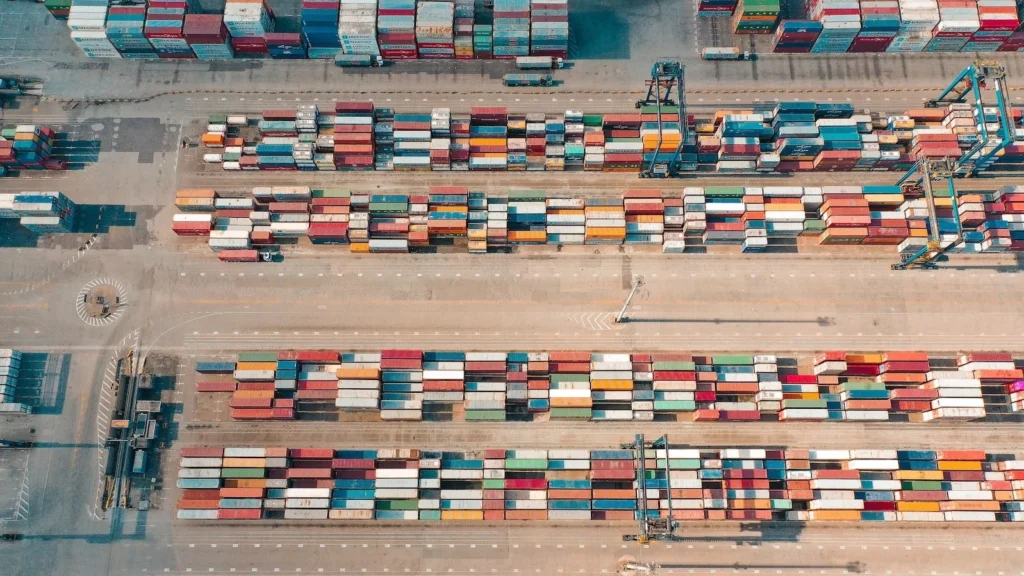
Smart Containers offer other advantages compared to electronic seals:
- for containers with IoT hardware embedded into the original design, there is no need for storing, sending, receiving and returning IoT devices, or for charging them as they can be powered by solar panels placed on the exterior of the containers or by electrical connection in the case of reefer containers;
- data management, data transfer, monitoring and even the virtual sealing is done in one place, the Smart Container’s control tower;
- the operating cost is low and included in the price paid by shippers; and
- there is no operational cost for Customs as the shipper is paying for the service.
5.Transport Management
AIoT, or the combination of Artificial Intelligence (AI) and the Internet of Things (IoT), plays a crucial role in transforming various industries, including transportation and in-plant logistics. In the context of in-plant logistics within a manufacturing facility, AIoT can bring about several advancements and improvements.
- Asset tracker
integrated circuits and reference designs offer the right combination of energy efficiency, simplicity and security using wide technology portfolio to build an asset tracker that monitors the location of assets over a cellular network.
RTLS asset tracking with SimpleLink™ Wi-Fi® devices:
Enabling smart management inventory
- RTLS asset tracking has developed from passive RFID tags to smart active, programmable tags that utilize Wi-Fi.
- RTLS asset tracking with Wi-Fi enables efficient inventory management for high value assets and allows assets to be tracked within a local network or remotely through the cloud.
- These RTLS tags can leverage the existing Wi-Fi infrastructure or can be deployed within a customized Wi-Fi network, which is commonly seen in hospitals and enterprise environments.
FEATURES :
- Industry’s lowest power Wi-Fi network processor with configurable power states for initialization
- Shutdown mode (1uA, 275 mSec – 1.375 Sec wake up time for external and internal clock respectively)
- Hibernate mode (4.5uA, 60mSec wake up time)
- Switchable two power profiles for 802.11 RTLS and Client interoperability
- Tag profile
- Transitions from hibernate/shutdown mode to transmission of user’s customized packets without connection to an AP
- Connected profile
- Connects to an AP and uses all OSI layers L6 through L1
- Tag profile
- Configurable Transceiver mode
- Bypass layer 2 through layer 6
- Select Wi-Fi channel
- Set TX power
- Wi-Fi rate – from 11b/g/n
- Wi-Fi and networking security features
- Secured Wi-Fi connection: including WPA2 enterprise
- Secured internet connection – HTTPS, SSL/TLS
- User data and code protection
- The SimpleLink SDK includes:
- Over-the-air library and example for software updates
- Plugins for multiple cloud solutions
- Industrial gateway
An industrial gateway is a hardware device designed with the ruggedness needed to withstand industrial environments. Just like other gateway devices, an industrial gateway manages traffic between otherwise isolated networks and subnetworks (subnets). Typically, the gateway controls the flow of information between floor-level devices and the outside world, as shown in figure 3.
Industrial gateways also perform protocol translation, enabling the communication between disparate interfaces. Protocol translation allows non-Ethernet-based components to be part of the industrial network and reach the outside world. This is one of the bases of the infrastructure needed in cloud-based solutions and IoT. Besides TCP/IP, some of the protocols that modern industrial gateways can work with are UDP (User Datagram Protocol), PROFINET, OPC-UA, and Modbus.
- The Industrial Gateway supports 12 protocols (the equivalent of 15 one-to-one protocol gateway devices). The more protocols you need bridged, the more savings you gain.
- The Industrial Gateway features 2 or 4 serial ports that operate simultaneously. This allows you to connect multiple devices with a single gateway. Additionally, each port can be configured with a different protocol.
- The Industrial Gateway features two Ethernet ports that supports multiple protocols, simultaneously. This allows you to connect multiple devices with a single gateway.
- The Industrial Gateway supports data transfers to and from any port, in any combination (Ethernet to Ethernet, Ethernet to Serial, Serial to Serial).
6.Scheduling and Dispatch
Artificial Intelligence (AI) and the Internet of Things (IoT) technologies can enhance scheduling and dispatch processes, leading to improved efficiency, reduced costs, and better overall operational performance. Here are some devices and technologies that can be employed for scheduling and dispatch in inplant logistics using AIoT:
- Bar code scanners :
Barcode scanners are widely used in industrial applications such as automatic tracking and quality control. Barcode scanners have advantages over other tracking methods, as they offer faster input speed, higher reliability, and the ability to scan a large amount of information while being flexible.
Renesas has a range of MCU/MPUs, power and analog devices that can be used for any barcode scanner solution, optimizing the solution to the specific need. This design utilizes the Renesas RZ/A2M MPU, which is designed for embedded artificial intelligence (e-AI) based imaging in smart appliances, networked cameras, service robots, scanner products, and industrial machinery that require high-speed image processing. It features a unique hybrid approach to image recognition and machine vision by combining proprietary DRP technology for fast pre-processing of image data and feature extraction.
The high-performance power and analog system utilizes Renesas’ PMIC, DC/DC, USB power supply controller and hub controller, OPA, timing, and an advanced digital light sensor.
System Benefits:
- High-speed embedded AI-based image processing device with Dynamically Reconfigurable Processor (DRP) technology
- Rich Renesas power and analog devices: PMIC, DC/DC, USB ASSP, operational amplifier, timing, and sensor
- QR code recognition with light proximity induction
- HDMI monitor support and AI-extensible features
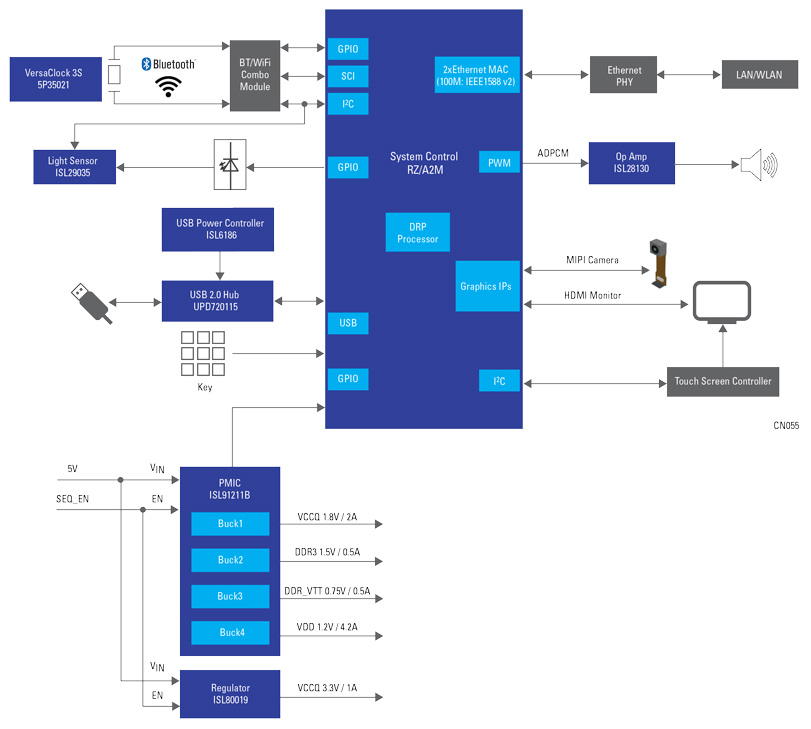
- Multi-Camera Tracking AI workflow
Giving perception to retail spaces often requires applying vision AI to many cameras covering multiple physical areas. The Multi-Camera Tracking AI workflow delivers multi-target multi-camera (MTMC) capabilities to allow application developers to easily create solutions that anonymously track shoppers from camera to camera. The workflow uses the NVIDIA DeepStream SDK, pretrained models, and new state-of-the-art microservices for re-identification and tracking.
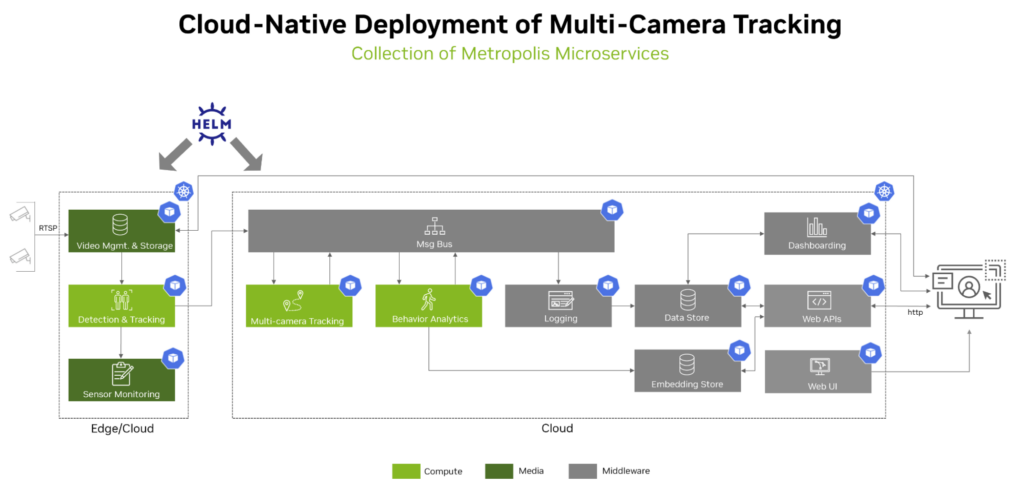
The MTMC workflow tracks and associates objects across cameras and maintains a unique ID for the object. Each object is tracked through visual embeddings/appearance rather than any personal biometric information, so privacy is fully maintained.
MTMC capabilities help bolster the security of self-checkout and is foundational for fully autonomous stores. The workflow can be trained to detect anomalous behavior. It can be deployed and scaled with Kubernetes and managed by Helm.
SOLUTIONS:
- Low-Power FPGAs:
Microchip FPGAs and SoC FPGAs consume up to 50% lower total power than competitive FPGAs. Our nonvolatile process delivers FPGA families that are live at power-up with minimal in-rush current, and significantly lower leakage than SRAM-based alternatives. Take it one step further; run a power benchmark with our power estimator. Seeing is believing.
- Fanless enclosures with small/no heat sink
- Increased thermal headroom for more compute capability
Features:
- SRAM FPGAs require a complex power up and reset sequencing. High in-rush currents occur during device initialization and configuration. Leveraging our SoC FPGAs simplifies sequencing requirements and components, reducing system cost, design complexity and board space.
- instant-on FPGAs assist in system startup tasks, system configuration and supervision. Instant-on functionality simplifies power-up sequence requirements with fewer components and lower cost while enhancing security and reducing initialization time.
- Fluorescent Lighting Technology:
provide accurate lighting and dimming control as well as add additional capabilities beyond that of traditional lighting solutions. The flexibility of these solutions allows for simplified attachment to existing designs or the development of full Switch Mode Power Supply (SMPS)-based intelligent solutions.
PIC® Microcontroller Attach to Basic Power Supply
- Simplified design-in
- Customizable features
- Simplified modifications via firmware updates
- Intelligent control capabilities
SMPS with PIC Microcontroller and Analog Products
- Increased microcontroller (MCU) integration
- Fully customizable
- Increased efficiency
- Power Factor Correction (PFC)
- Flexible topologies
- Simplified modifications via firmware updates
- Closed-loop control feedback
- High-performance PWM and current control variation
- Intelligent control capabilities
Ultra-Low Power Wi-Fi Modules for Battery Powered IoT Devices
DA16200 modules are the perfect complement to the DA16200 ultra-low power Wi-Fi SoC. They deliver the same long battery life and low power consumption but in a convenient form factor. The modules are complete with all required components and are regulatory certified by the FCC, IC, CE and other regulatory bodies.
The fully integrated module consists of the DA16200 SoC, 4MB flash memory, RF components including crystal oscillator, RF lumped filter, and either a chip antenna or a connector for an external antenna.
The module has 37 pins including GPIOs, JTAG, RTC control, UART, power input, and the 32.768kHz crystal.